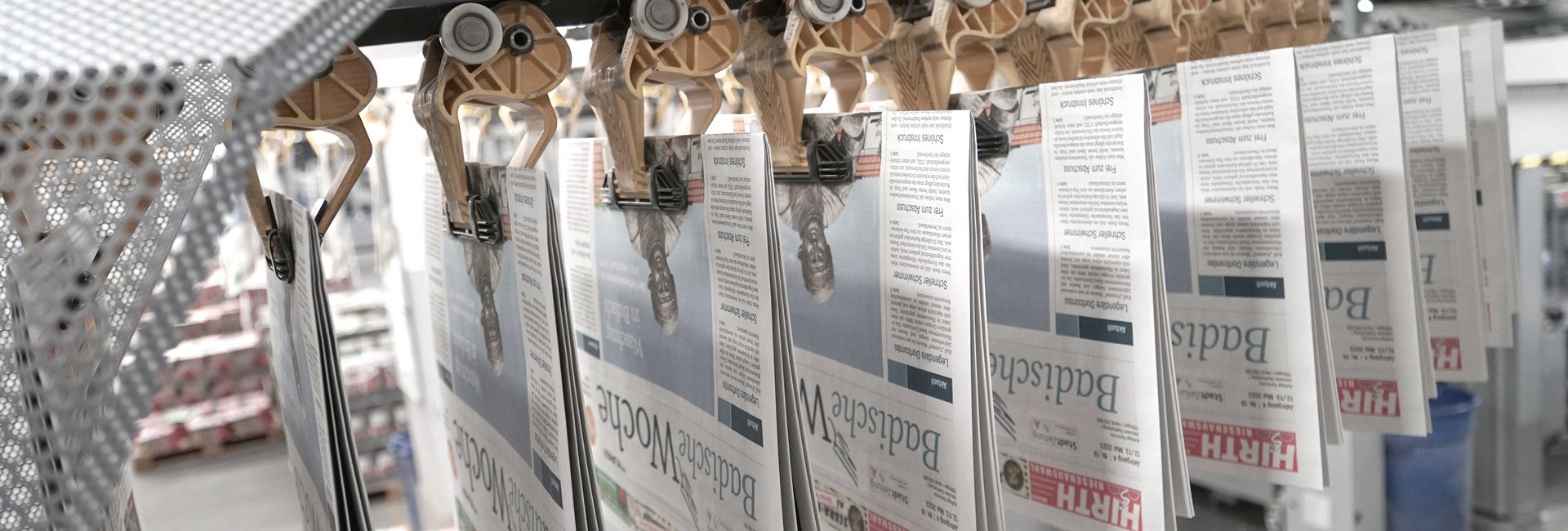
- Home
- Actualités et newsletter
- More efficiency through EasySert plug-in technology
More efficiency through EasySert plug-in technology
Badische Neueste Nachrichten celebrated its 75th anniversary on March 1, 2021, the same year Badische Tagblatt GmbH in Baden-Baden was acquired. Badendruck, the technical operation of the BNN, has been located in Karlsruhe-Neureut since 1972, where the entire company was later moved. The print shop building has therefore already housed several generations of printing and finishing technology. Most recently, new presses were installed here in 2012 - of the Koenig & Bauer Commander CT 6/2 type, each with two 24-page printing towers, which were unloaded onto two Ferag MSD lines. Since then, printing has also taken place in the Rhenish format (350 x 510 mm).
BNN's print shop, with its AV, prepress, press, post press and maintenance/maintenance departments, employs around 100 full-time and part-time staff - plus temporary workers. Newspapers, advertising journals and magazines are produced. The main product is the regional daily newspaper Badische Neueste Nachrichten, of which around 125,000 copies are currently printed six times a week in 10 sections. In addition, the company produces around 600,000 of its own advertising journals per week.
The market changed
Along with the new printing technology, two Ferag MSDs with 7 feeders each had also come into the house in 2012 - a common configuration at the time of the investment. But just two years later, a dynamic development began in the advertising market in Germany, towards significantly more newspaper inserts. The development continued until the start of the Covid pandemic in 2020, presenting the bathroom printing team with ever-increasing production challenges.
Matthias Köhler, Head of Production Coordination: "Since the seven feeders were often not sufficient, we had to split print production into preliminary and main products, especially for the advertising sheets. Then many different wraps were created for insertion into the VP - a very complex and error-prone principle and a relatively ineffective production." The production windows were getting longer and longer; on the other hand, the increasing demand for small-size inserting meant that the JetFeeder feeders had to be constantly rebuilt and the actually very high speed of the MSD inserting drums could not be exploited at all.
The general slump in advertising in the first few months of the Covid pandemic, also had consequences for the advertising papers produced in Karlsruhe: The already existing trend towards bundling and merging intensified significantly. Issues that had previously appeared in the middle of the week were partly discontinued and partly merged with the weekend editions. This had a corresponding impact on the already full production days from Thursday to Saturday. Matthias Köhler: "This clearly showed us that we needed a more efficient system with higher net output. We saw that we had to act".
In addition to a reorganization of the product portfolio, the systems under consideration were evaluated, and the contracts with Ferag were signed in January 2022.
Future orientation and flexibility
Future orientation and flexibility were at the top of the requirements profile: the new line consisting of EasySert inserting reel, FlyStream gathering line and 23 feeders, two of which for automatic feeding from the reel, had to be equipped for everything. Matthias Köhler: "We can do Tapefix production, so if necessary we can form insert collections without carrier product. We also have all opening types available - blast air, vacuum and prefold opening. And we can produce trimmed products or make self-sufficient jacket productions via the manual feeder, i.e. put inserts in inserts."
The new concept included the reconstruction of the compensating stacker connection and the package removal. Three of the six MTS compensating stackers were previously permanently assigned to each mailroom line. However, if one stacker failed, the output of the corresponding production line quickly fell to its knees. With the new concept, all six compensating stackers can now be assigned to the two mailroom lines as required, i.e. one line can be run on five stackers and the other on just one. This is also a building block for greater flexibility. The two previous PKT lines for outbound transport therefore also had to be combined to form an "eight".
In May 2022, the implementation of the project began with the step-by-step dismantling of the MSD line. Parts that were in good condition were reused for the new production line. Unlike many other plants, there was no free space available in Karlsruhe where the new line could have been built before the old production line was taken out of service. For a certain time, the MSD was still able to make its contribution - when there were no inserts in the product. From mid-July, however, production was then only feasible on one line in the mailroom for several weeks.
"An absolutely good job"
The clear requirement for Ferag was that the project had to be completed by the beginning of the "pre-Christmas period". And they succeeded: "From the beginning of November, we were able to go into full production on the new line. And it wasn't easy," says Matthias Köhler. For example, there were various supply bottlenecks for electrical components.
But both the Ferag project management and the BNN employees involved "did an absolutely good job," praises Matthias Köhler. "It was top-notch - very well timed and professional in its implementation. The project was completed to our complete satisfaction." The most important goals were achieved very quickly: Production time was reduced for practically all productions, the company is now well organized thanks to the Optimizer software from Ferag, and it is also significantly faster and achieves a higher net output, Matthias Köhler sums up.