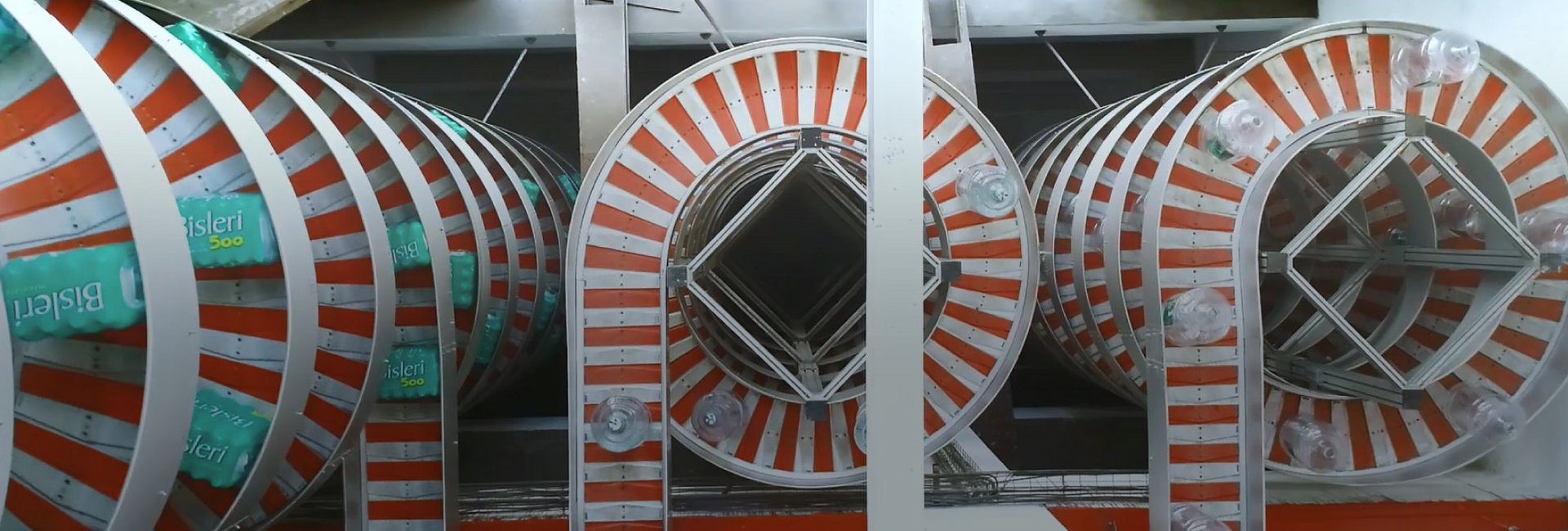
- Home
- News & Newsletter
- Vertical end-of-line solution for a mineral water bottler in Mumbai
Vertical end-of-line solution for a mineral water bottler in Mumbai
The name "Bisleri" derives from the Italian entrepreneur Felice Bisleri, owner of the "Sorgenti Angelica" in Nocera Umbra. He already expanded to India in 1965. Four years later, the Parle Group took over the company. Since then it has seen unprecedented growth, becoming by far the leading soft drink brand on the Indian subcontinent. Just a few months ago, in time for the company’s 50th anniversary, Bisleri opened a state-of-the-art bottling plant at its Mumbai headquarters equipped with every imaginable technical refinement. Not only is the company particularly proud of this, it also boasts of being “the world’s first and only vertical mineral water producer.”
The cutting edge in mineral water bottling: high efficiency from top to bottom and back again
“Vertical” in this case refers primarily to the conveyor technology linked to the automatic filling machinery: two end-of-line systems supplied by Ferag, which consist of two deniway plate chain conveyor lines with chain lengths of 290 and 170 metres respectively. Three helices form the highlight here, spiralling their way up and down within a highly confined space. The first of these is part of the longer conveyor section and spans a record-breaking height of 20 metres. Its job is to convey shrink-wrapped packs of PET bottles with various capacities (250 ml × 24 bottles, 250 ml x 48 bottles, 500 ml × 24 bottles, 1000 ml × 12 bottles, 2000 ml × 9 bottles) at one metre per second through five floors to the warehouse and shipping area down on the second basement level. The other two spirals, eleven and six metres tall, form a conveyor duo as part of a second, shorter line dedicated exclusively to 5 litre and 20 litre bulk containers. After filling, they travel vertically down the second spiral to the first basement level. On the third spiral meanwhile, empty containers ascend from thorough external cleaning on the ground floor to the rinsing and filling machines at the 1st floor of the building. The Ferag technology implemented in Mumbai is capable of very tight curve radii and thus underlines the enormous flexibility of spiral conveyors. These can bridge very large height differences while requiring little space: the deniway spirals at Bisleri have a diameter of just 2.5 metres. Added to this is their high energy efficiency: each line requires only one motor, thanks to extremely smooth-running technology invented by the Swiss that works on the principle of “rolling, not sliding”. The load-governed drive system is designed so that each of the two conveyor sections can handle a total transport weight of up to 1.45 tons per minute. This translates to 100 packaging units per minute, or 6000 per hour.
Robust conveyor technology proves itself to the full in a hot and humid monsoon climate
Although the Swiss conveyor technology functioned smoothly right from the start – deniway is, after all, a classic in the Ferag line-up – there were several challenges for the project engineers on site in Mumbai to overcome prior to commissioning. The greatest was perhaps a tight time schedule, which meant delivering and installing the deniway modules in the midst of the rainy monsoon season: extremely unfavourable in European terms. “We kept our sporting cool about it. After all, like this we could immediately show the customer that our systems are sufficiently robust to withstand the hot and humid climate and perform reliably,” recollects Kawal Arora, Managing Director of WRH Global India, the Ferag marketing subsidiary involved. The installation of the system components in the multi-storey building ultimately proved to be unproblematic as well. Working in the fitters’ favour was the fact that Ferag has tuned the deniway system from the outset for easy integration with existing properties. And thanks to the Swiss systems’ highly modular nature, installations are also easy to modify and scale.
No dirt ingress: deniway guaranteed suitable for food
There was indeed another factor central to the decision in favour of Ferag technology: cleanliness. As a beverage manufacturer, Bisleri attaches great importance not only to the high quality of its products, but also to impeccable hygiene in production. The starting product obtained from ground or river water is freed of germs and microbes in a multi-stage ozone treatment process, filtered several times and then stripped of undesired minerals by reverse osmosis. Minerals are subsequently put back in again, but in precisely defined measure. Four high-speed machines fill the resulting mineral water under stringent controls. Even the screw caps of PET and water dispenser bottles are disinfected by ozonation during the filling process. So it goes without saying that the conveyor technology also has to meet the Indian mineral water producer’s strict criteria. The conveyor that automatically loads the filling machines with empty, freshly rinsed containers via a third deniway spiral must not introduce any dirt into this highly sensitive area. The same applies to peripherals downstream of the filling machines. Both the electromechanical pusher that feeds conveyed goods onto the descending deniway conveyor section and the line itself must be suitable for transporting packaged foodstuffs. Which is to say: Bisleri only considered conveyor technology with high-quality, abrasion-free and easily cleaned components. Also taboo: systems requiring lubrication. deniway technology meets all these criteria with flying colours. Otherwise it would not have been in long-time use by other food producers such as Nestlé and Mondelēz.
At the end of the line, down in shipping and warehousing, another decisive advantage of the Ferag system becomes apparent. As Arora points out, deniway technology is unbeatable in one respect: “It forms one of the most efficient interfaces between upstream production and palletizers currently available on the market.”